技术支持案例
案例一
收到客户诉求及失效情况 → 分析工况,失效情况、提出设计方案 → 应用设计优化方案 → 确认方案定稿设计 → 迅速投产生产制作 → 验收交付 → 跟进效果验证
140阀门设计压力22.45MPa,设计温度510℃,最大关闭压差22.45MPa,工作中入口压力20.52MPa,出口压力0.86MPa,工作温度410℃,正常情况下平均流量为8000kg/h(开关时间各半,因此开启时流量为16000kg/h)。
流经阀门的介质为LPH热高分油渣,密度为1200kg/m3,动力粘度为50mPa·s,固体含量为53.6%,气化量为1.5%~10%。含有固体颗粒的流体介质对阀芯冲刷侵蚀,使阀芯破坏,导致阀门失效。根据Preston磨削经验公式,阀芯的冲刷侵蚀与阀芯周围的流体速度和压力成正比。
案例二
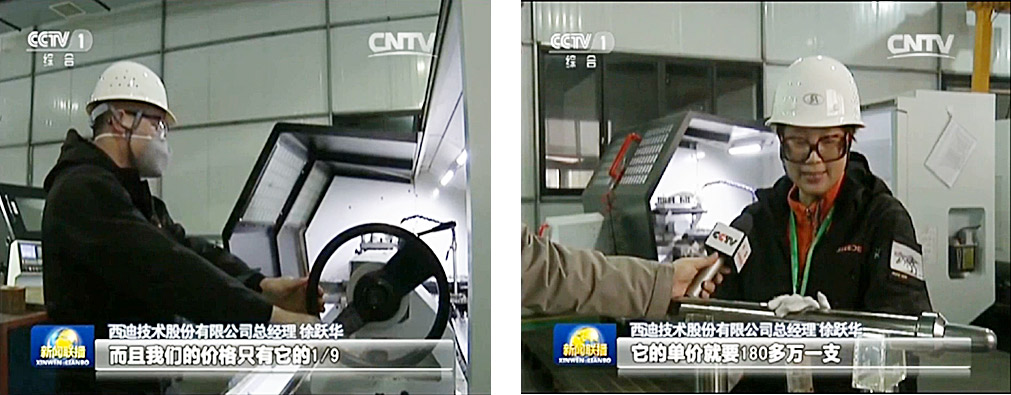
背景:
人类石油需求量逐年增多,石油开采储量在逐年下降,煤制油技术的开发解决了这一能源紧迫性问题。但煤制油面临的苛刻环境使其对材料和装备的要求非常高,单向阀作为煤制油技术的关键核心零部件需求量高速增长,但早年单向阀的研发生产被德国所垄断,单价高昂,而且使用寿命仅1到3小时,这些都严重制约了煤制油技术的发展。
解决方案:
西迪公司为了满足煤制油领域广大客户对单向阀的大量需求,潜心研究单向阀生产技术,实现自主化生产煤制油设备关键零部件,打破了德国垄断生产局面,为煤制油技术做出重大贡献。
取得成效:
自主化生产单向阀实现了将价格压缩至原来的1/9,节省了成本,使用寿命也大大提高,被央视新闻联播报道“匠心创新,亮出中国制造新名片。”